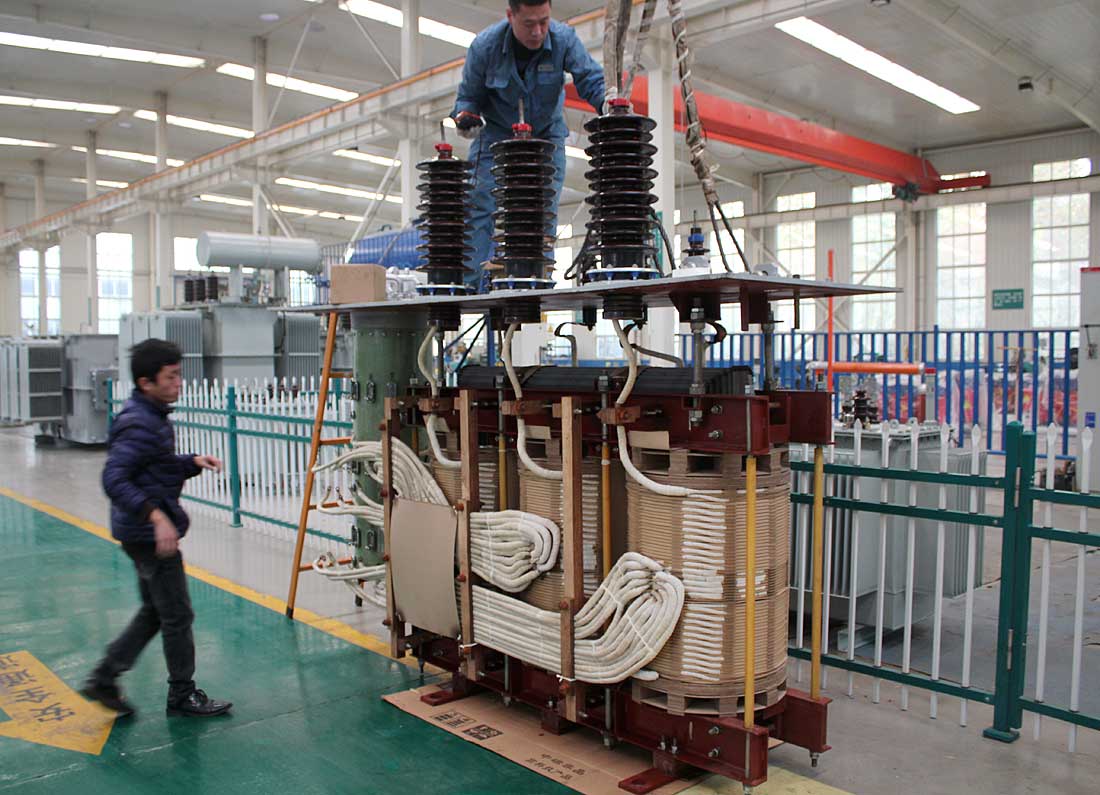
Is the distribution transformer damaged? The reason analysis and solutions are here!
This paper details the analysis and solutions for the damage of distribution transformers, including the common faults and abnormal phenomena of distribution transformers in power transmission and operation, the causes of damage to distribution transformers (especially judging faults from the sound of transformers), and the damage to distribution transformers. solution.
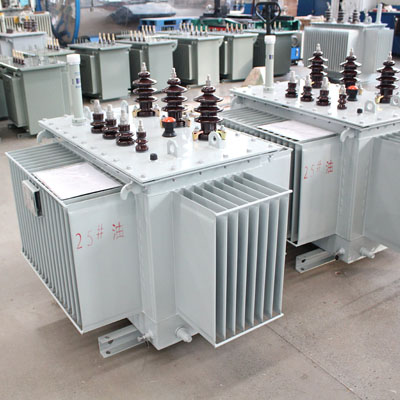
■ The common faults and abnormal phenomena of distribution transformers in power transmission and operation are:
- When the transformer is powered on or tested after the outage, it is often found that the voltage is abnormal, such as two-phase high and one-phase low or the indication is zero; The electrical equipment is burnt due to excessive voltage;
- The high-voltage fuse is blown and cannot be powered on;
- The transformer cannot be powered on after the thunderstorm;
- The sound of the transformer is abnormal, such as “squeak” or “crack” sound; during operation, it makes a sound such as a frog’s “wow”;
- The high-voltage terminal is burned out, and the high-voltage bushing has serious damage and flashover traces;
- Under normal cooling conditions, the temperature of the transformer is abnormal and continues to rise;
- The color of the oil changes too much, and there is carbon in the oil;
- The transformer emits a roar and sprays oil from the safety airway and the oil conservator.
■ Causes of damage to distribution transformers
- Overload
First, with the improvement of people’s life, the power consumption generally increases rapidly. The original distribution transformer has a small capacity, and the small horse-drawn cart cannot meet the needs of users, resulting in the overload operation of the transformer. Second, due to seasonal and special weather and other reasons, the power consumption peaks and the distribution transformers are overloaded. Due to the long-term overload operation of the transformer, the internal components, coils and oil insulation of the transformer are aged, and the load of the transformer is mostly distributed seasonally and temporally, especially in the rural busy season. The distribution transformer will be used under overload or full load , and it is used at light load at night, the load curve difference is very large, the operating temperature is as high as 80 ℃, and the minimum temperature is 10 ℃. Moreover, from the perspective of the maintenance of rural transformers, the average moisture at the bottom of each transformer is more than 100 g, which is precipitated from the oil by the breathing air that expands and contracts when the transformer oil heats up and contracts. Second, the lack of oil inside the transformer reduces the oil level, causing the contact surface between the insulating oil and the air to increase, which accelerates the entry of moisture in the air into the oil surface and reduces the internal insulation strength of the transformer. When the insulation is reduced to a certain value, breakdown occurs inside the transformer. Short circuit fault.
- Illegal refueling of distribution transformers
An electrician refueled the running distribution transformer. After 1 hour, the fuse of the transformer’s high-voltage drop-out switch blew two phases, and there was slight fuel injection. After on-site inspection, it needed to be overhauled. The main reasons for the transformer burnout are:
◉ First, the newly added transformer oil is inconsistent with the oil type in the transformer box. There are several oil bases for transformer oil, and different types of oil bases cannot be mixed in principle;
◉ Second, there was no power failure when refueling the distribution transformer, resulting in the mixing of the hot and cold oil inside the transformer, the circulating oil flow accelerated, and the water at the bottom of the device was taken up and circulated to the inside of the high and low voltage coils, causing the insulation to drop and cause a breakdown and short circuit. ;
◉ The third is adding substandard transformer oil.
- Improper reactive power compensation causes resonance overvoltage
In order to reduce the line loss and improve the utilization rate of the equipment, it is stipulated in the “Rural Low Voltage Power Technical Regulations” that the reactive power compensation device should be used for the distribution transformer with a capacity of more than 100 kVA. If the total capacitive reactance and the total inductive reactance of the running line are equal to the improper compensation, ferromagnetic resonance will be generated in the running line and equipment, causing overvoltage and overcurrent, and burning distribution transformers and other electrical equipment.
- System ferroresonance overvoltage
The 10 kV distribution lines in the rural network are inconsistent in length, distance to ground, and wire specifications, and when operating parameters such as distribution transformers, electric welding machines, capacitors, and the switching of large loads change greatly, or the 10 kV neutral The single-phase intermittent grounding of the point-ungrounded system may cause resonance overvoltage in the system. Once the system resonance overvoltage occurs, the lighter one is to blow the distribution transformer’s high-voltage fuse, and the more severe case will cause the distribution transformer to burn, and in some cases, the distribution transformer bushing will flash over or explode.
- Lightning overvoltage
The distribution transformer must install qualified arresters on the high and low voltage sides according to the regulations to reduce the damage of lightning overvoltage and ferromagnetic resonance overvoltage to the high and low voltage coils or bushings of the transformer. The main reasons for damage to distribution transformers are:
◉ First, the installation test of the arrester does not meet the requirements. The installation of the arrester is generally three arresters and only one point is grounded. During long-term operation, due to long-term disrepair, wind and rain will cause serious rust, climate change and other special circumstances cause the grounding point to be disconnected or Poor contact, when there is lightning overvoltage or system resonance overvoltage, the transformer will be broken down because the ground cannot be released and stepped down in time;
◉ Second, because most transformers are insured by insurance companies, the resulting emphasis is on insurance company compensation and less on maintenance management. Some users think that the transformer is insured, and it does not matter whether the arrester is installed or not, whether it is tested or not, anyway, the transformer is broken. The insurance company is responsible for compensation, and it is also an important factor in the serious damage of distribution transformers over the years;
◉ The third is to only pay attention to the installation test of the arrester on the high-voltage side of the transformer, and despise the installation test of the arrester on the low-voltage side. Because the arrester is not installed on the low-voltage side of the transformer, when the low-voltage side of the transformer is struck by lightning, the inverter will generate an impact on the high-voltage side coil of the transformer at the same time. , the low-voltage side coil may also be damaged.
- Secondary short circuit
When the distribution transformer is short-circuited twice, a short-circuit current several times or even dozens of times higher than the rated current is generated on the secondary side, and a large current is also generated on the primary side to offset the demagnetization of the short-circuit current on the secondary side. On the one hand, such a large short-circuit current will generate huge mechanical stress inside the transformer coil, which will cause the coil to compress, the main and auxiliary insulation will loosen and fall off, and the coil will deform. On the other hand, due to the existence of short-circuit current, the temperature of the primary and secondary coils rises sharply. At this time, if the primary and secondary fuses are improperly selected or replaced with aluminum-copper wires, the transformer coils may be burnt out quickly.
- Poor crimping of the tap changer
First, the quality of the tap changer itself is poor, the structure is unreasonable, the spring pressure is not enough, the dynamic and static contacts are not in complete contact, the insulation distance between the dislocated dynamic and static contacts becomes smaller, and discharge or short circuit occurs between the two taps, which will quickly burn out. Transformer tap coil or the entire winding; the second is man-made reasons. Individual electricians are not clear about the principle of no-load voltage regulation. After voltage regulation, the dynamic and static contacts are partially in contact or due to the long-term operation of the transformer tap changer contacts, the static contacts are dirty. Contact Poor discharge and ignition cause the transformer to burn out.
- The respirator hole is blocked
Generally, “breathers” are installed on the oil pillows of transformers above 50 kVA. The cover of the “respirator” is generally a transparent glass cylinder with a “moisture absorbing agent” inside, which is easily broken during handling, so in general, the manufacturer does not install it when it leaves the factory, and installs a “respirator” on the transformer oil pillow. Use screws to block a “small square iron plate” at the position of the “moisture absorber” to prevent moisture. The “small square iron plate” should be removed in time when it is put into operation. If it is not removed and replaced with a “respirator” in time, due to the continuous generation of heat after operation, the insulating oil will be heated and expanded, the pressure in the transformer will rise, the oil circuit cannot be circulated, and the heat will be dissipated. If you don’t go out, the heat of the iron core and the coil is getting higher and higher, the insulation performance is degraded, and eventually the transformer is burned out.
- Others
Common problems in the daily operation and maintenance management of distribution transformers:
◉ First, in the process of maintenance or installation, when tightening or loosening the conductive rod nut of the transformer, the conductive rod rotates with it, which may cause the soft copper sheets drawn from the secondary side to collide, resulting in a short circuit between phases or the lead of the primary side coil is broken;
◉ Second, during maintenance on the transformer, objects or tools are accidentally dropped, and the bushing is damaged, which may cause flashover and grounding in light, and short circuit in heavy;
◉ The third is that the phase is not checked after the parallel operation of the transformer is repaired, tested or replaced, and the phase sequence is wrongly connected due to random wiring. After the transformer is put into operation, a large circulating current will be generated and the transformer will be burned; The anti-theft metering box, due to space problems and poor process crimping, some are directly wrapped with wires, resulting in excessive contact resistance of the low-voltage side wiring, heating and ignition during heavy load operation, causing the conductive rod to burn out.
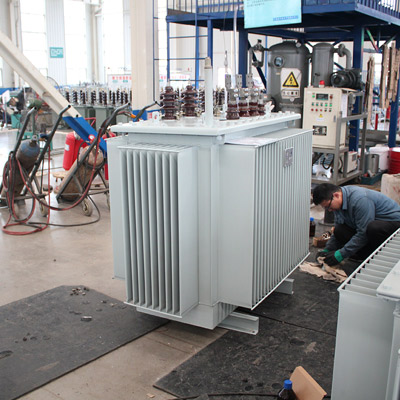
■ TIPS: Judging the fault from the sound of the transformer
- The sound when the phase is missing When the transformer is out of phase, if the second phase is blocked, there will be no sound when the second phase is sent, and there will be a sound when the third phase is sent; if the third phase is blocked, the sound will not change, and the second phase same time. There are generally three reasons for the lack of phase: ①The power supply lacks one phase of electricity; ②The transformer high voltage fuse blows one phase; ③Due to the careless transportation of the transformer and the thin high-voltage leads, the vibration and disconnection are caused (but not connected to the case).
- The sound when the phase is missing When the transformer is out of phase, if the second phase is blocked, there will be no sound when the second phase is sent, and there will be a sound when the third phase is sent; if the third phase is blocked, the sound will not change, and the second phase same time. There are generally three reasons for the lack of phase: ①The power supply lacks one phase of electricity; ②The transformer high voltage fuse blows one phase; ③Due to the careless transportation of the transformer and the thin high-voltage leads, the vibration and disconnection are caused (but not connected to the case).
- The voltage regulating tap changer is not in place or the contact is poor. When the transformer is put into operation, if the tap changer is not in place, it will make a loud “chirp” sound, which will cause the high-voltage fuse to blow in severe cases; if the tap changer is in poor contact, it will Produces a slight “squeak” spark discharge sound, once the load increases, it may burn out the contacts of the tap changer. In this case, the power outage should be promptly repaired.
- Falling foreign objects and loosening of the through-core screw When the through-core screw of the transformer clamping the iron core is loose, there are nut parts left on the iron core or small metal objects are dropped into the transformer, the transformer will make a “ding-ding” percussion sound or “” Hu…hu…” The blowing sound and the “squeaky” sound like a magnet sucking a small gasket, but the voltage, current and temperature of the transformer are normal. This kind of situation generally does not affect the normal operation of the transformer, and can be dealt with when the power is cut off.
- Dirty and cracked high-voltage bushings of transformers When the high-voltage bushings of transformers are dirty and the surface enamel falls off or cracks, surface flashover will occur, and a “hissing” or “chirp” sound will be heard, which can be seen at night spark.
- Transformer’s iron core grounding disconnection When the transformer’s iron core grounding disconnection, the transformer will produce a slight discharge sound of “beep peeling beep peeling”.
- When the internal discharge is used for power transmission, the crisp sound of “crackling” is heard, which is the discharge sound of the conductive lead to the transformer shell through the air; if the dull “crackling” sound is heard through the liquid, it is the conductor passing through the transformer oil surface Discharge sound to the enclosure. If the insulation distance is not enough, the power should be cut off and the core should be checked, and the insulation should be strengthened or an insulation partition should be added.
- The external line is disconnected or short-circuited. When the line is disconnected at the connection of the wire or at the T connection, it is connected and disconnected when the wind blows, and arcs or sparks occur when contacting. When the low-voltage line is grounded or a short-circuit accident occurs, the transformer will make a “boom” sound; if the short-circuit point is close, the transformer will make a roar like a tiger.
- Transformer overload When the transformer is overloaded seriously, it will emit a low “hum” sound like a heavy-duty aircraft.
- High voltage When the power supply voltage is too high, the transformer will be over-excited, and the sound will increase and become sharp.
- High voltage When the power supply voltage is too high, the transformer will be over-excited, and the sound will increase and become sharp.
■ Measures to solve the damage of distribution transformers
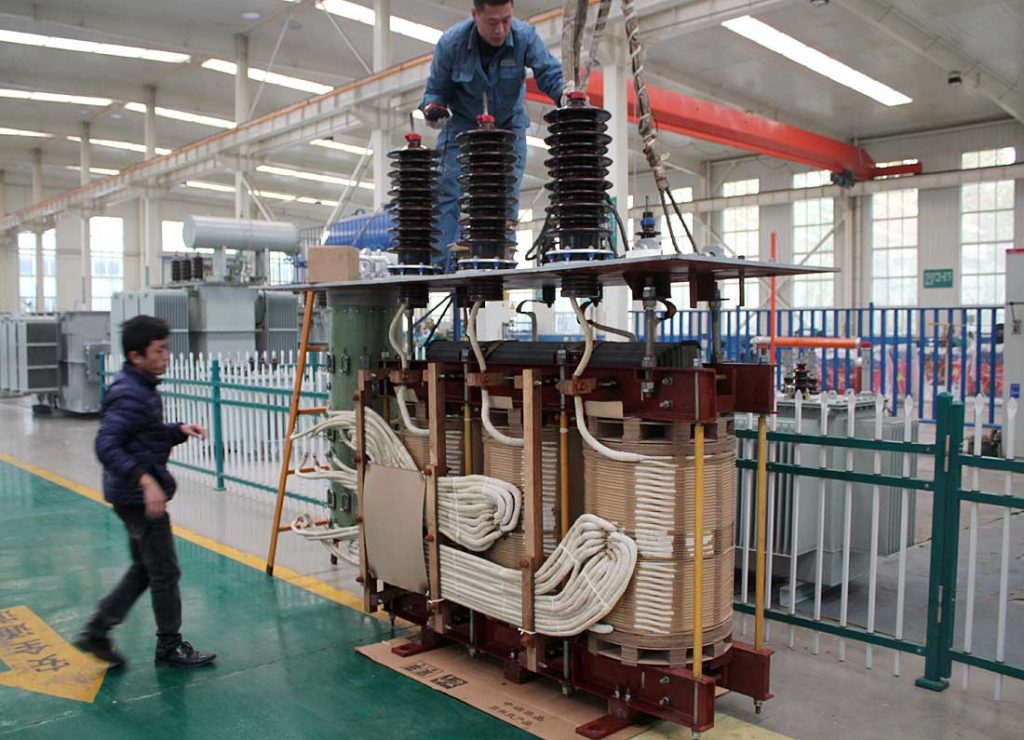
According to the analysis of the reasons for the damage of the above distribution transformers, a considerable part of the damage of distribution transformers can be avoided, and some of them can be eliminated in the bud as long as the inspection of equipment is strengthened and the safety rules and regulations are strictly enforced. Specific measures are as follows.
1.Do a good job of checking and testing before running
On-site inspection must be carried out before the distribution transformer is put into operation. The main contents are as follows:
- Whether the oil level gauge on the oil pillow is in good condition, and whether the oil level is clear and on the oil level line consistent with the environment. If the oil level is too high, after the transformer is put into operation with a load, the oil temperature will rise, and the oil expansion is likely to cause the oil to overflow from the breathing apparatus connecting pipe on the top of the oil pillow; if it is too low, it will be lightly loaded in winter or out of service for a short time. , the oil level may drop to the point where the oil level gauge cannot see the oil level.
- Whether the casing, oil level gauge, oil discharge valve, etc. are well sealed, and whether there is oil leakage. Otherwise, when the transformer is loaded, more serious leakage will occur in the thermal state.
- Whether the explosion-proof tube (breathing airway) is unobstructed and intact, and whether the hygroscopic agent of the respirator fails.
- Whether the grounding of the transformer shell is firm and reliable, because it directly protects the transformer.
- Whether the primary and secondary outlet bushings of the transformer and their connection with the wires are good, and whether the color is correct.
- Whether the nameplate on the transformer is consistent with the required transformer specification. Such as the voltage level of each side, the capacity of the transformer and the position of the tap changer.
- Measure the insulation of the transformer. Use a 1000~2500V megohmmeter to measure the insulation resistance of the primary and secondary windings of the transformer to ground (when measuring, the non-measured winding is grounded), as well as the insulation resistance between the primary and secondary windings, and record the ambient temperature during measurement. The allowable value of insulation resistance is not rigidly specified, but it should be compared with historical conditions or original data, and should not be lower than 70% of the factory value (when the temperature of the tested transformer is different from the temperature tested by the manufacturer, it should be converted to the same temperature compare again).
- The mutual difference of the DC resistance of each phase of the transformer should be less than 4% of the average value, and the mutual difference of the DC resistance between the lines should be less than 2% of the average value.
If the above inspections are all qualified, insert an alcohol thermometer above 100 ℃ into the temperature measuring hole of the transformer, so as to monitor the operating temperature of the transformer at any time, and then air-drop the transformer (without load) to check whether the electromagnetic sound is abnormal, and measure the secondary side. Whether the voltage is balanced, such as balanced, indicates that the transformer ratio is normal, there is no inter-turn short circuit, and the transformer can operate normally with load.
2.Precautions during operation
The following must be done in the operation and management of distribution transformers:
- In the process of using the distribution transformer, it is necessary to regularly check whether the three-phase voltage is balanced. If there is a serious imbalance, measures should be taken to adjust it in time. At the same time, the oil level, temperature and oil color of the transformer should be checked frequently, whether there is leakage, and whether the color of the desiccant in the respirator has changed.
- ) Regularly clean the dirt on the distribution transformer, take anti-fouling measures if necessary, install the bushing anti-fouling cap, check whether the bushing has flashover discharge, whether the grounding is good, and whether there is disconnection, desoldering, or fracture. Shake the ground resistance.
- When the screw of the electric transformer is disassembled and assembled, it must be strictly dealt with, and it can be put into operation after confirmation. Reasonably choose the wiring method of the secondary side conductors, such as the use of copper-aluminum transition clips. Apply conductive paste on the contact surface to increase the contact area and conductivity, and reduce oxidation and heat generation.
- Install lightning arresters on the primary and secondary sides of the distribution transformer, and ground the arrester grounding down-conductor, the transformer shell, and the neutral point of the secondary side. The oil temperature of the upper layer should not exceed 85 ℃ frequently, and the maximum should not exceed 95 ℃ (inserting a thermometer into the thermometer on the side of the distribution transformer can measure the instant temperature of the operating transformer at any time), and it should not be overloaded for a long time. However, when the daily load factor is less than 1 (the ratio of the daily average load to the maximum load) and the oil temperature of the upper layer does not exceed the allowable value, the operation can be carried out according to the provisions of normal overload, and the total overload value should not exceed 20% of the transformer) . When the insulation (insulating medium such as oil) in the transformer is to double the aging rate, the service life should be reduced accordingly. Therefore, prolonged overload operation must be avoided.
- Avoid unbalanced operation of three-phase loads. The unbalanced operation of the three-phase load of the transformer will cause the unbalance of the three-phase current, and the three-phase voltage will also be unbalanced at this time. The transformer with unbalanced three-phase load should be regarded as the load with the maximum current. If the three-phase maximum unbalanced current or the neutral current measured during the maximum load period exceeds 25% of the rated current, the load should be placed at the three-phase load. Interphase reallocation.
- Prevent secondary short circuit. The secondary short circuit of the distribution transformer is the most direct cause of transformer damage, and the key to a reasonable selection of distribution transformers is. Under normal circumstances, the high-voltage side (drop fuse) fuse of the distribution transformer is selected within 1.2 to 1.5 times the rated current of the high-voltage side, and the low-voltage side is selected according to the rated current. In this case, even if a low-voltage short-circuit fault occurs, the fuse can The transformer plays a proper protective role.